Creating a Welding WPS: Step-by-Step Instructions for Professionals
Wiki Article
Achieving Welding Excellence: Revealing the Keys of WPS Application and Optimization
In the world of welding, attaining excellence is a search that rests on the thorough implementation and optimization of Welding Procedure Specs (WPS) These fundamental papers function as the backbone of welding procedures, determining the specifications and treatments needed for producing premium welds consistently. However, the tricks to opening the full potential of WPS exist not only in understanding its importance but also in understanding the details of its implementation and optimization. By diving into the crucial elements, approaches, difficulties, and best practices associated with WPS, a globe of welding excellence waits for those that agree to explore its depths.Importance of WPS in Welding
The Value of Welding Procedure Requirements (WPS) in the welding industry can not be overemphasized, serving as the foundation for making sure consistency, high quality, and safety in welding procedures. A WPS offers detailed directions on just how welding is to be accomplished, consisting of vital variables such as materials, welding procedures, joint design, filler metals, interpass and preheat temperatures, welding currents, voltages, traveling speeds, and more. By adhering to a distinct WPS, welders can maintain uniformity in their job, leading to constant weld quality across various jobs.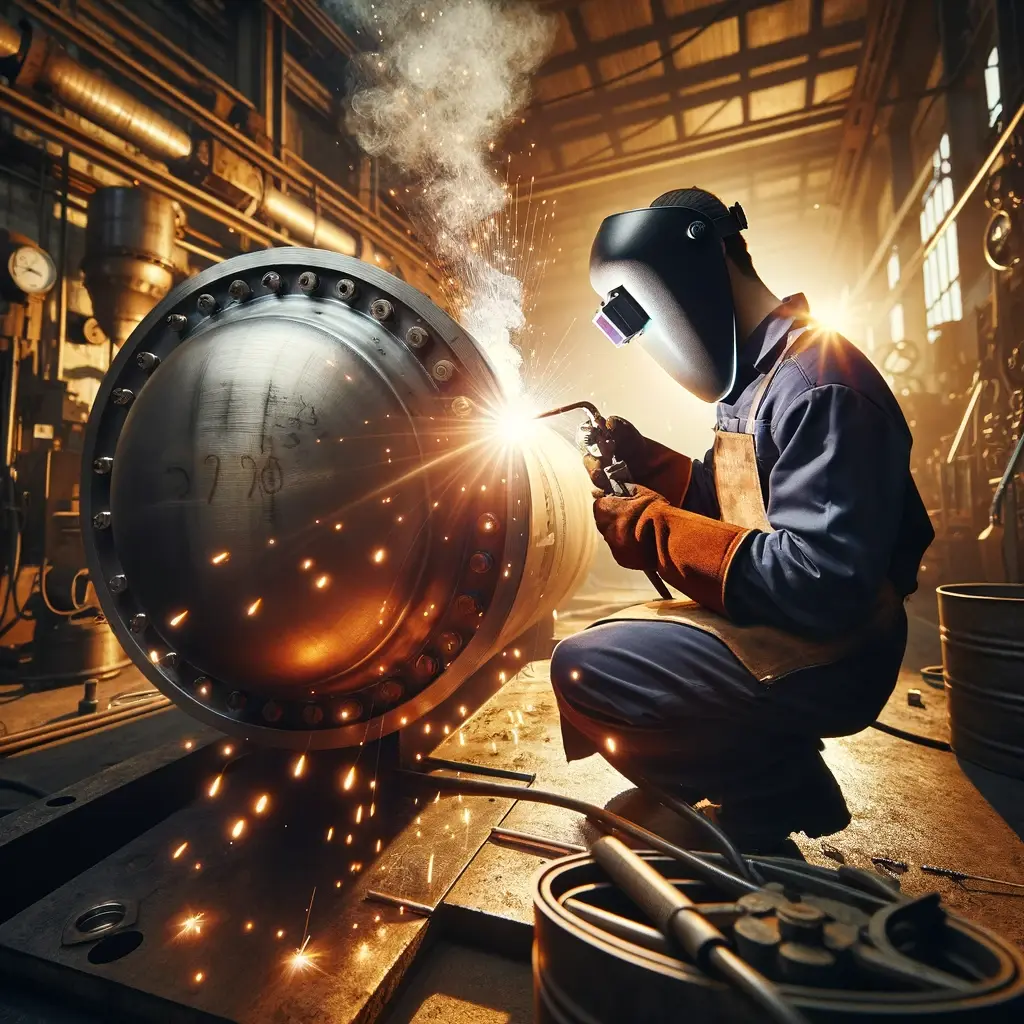
Secret Components of WPS
Talking about the indispensable elements of a welding treatment specification (WPS) is important for understanding its role in welding operations. An extensive WPS consists of numerous essential components that lead welders in accomplishing top quality and uniformity in their work. One important aspect of a WPS is the welding process spec, which lays out the specific welding processes to be made use of, such as gas tungsten arc welding (GTAW) or protected steel arc welding (SMAW) Additionally, the WPS includes information on the welding products, such as the kind and specifications of the base steel and filler metal to be utilized. The WPS likewise specifies necessary variables like welding criteria, preheat and interpass temperature needs, and post-weld warmth therapy procedures. In addition, it includes details on joint style, fit-up, and any unique strategies or precautions required for the welding operation. By including these essential components right into the WPS, welding treatments can be standardized, ensuring high quality, effectiveness, and safety and security in welding operations.Techniques for WPS Optimization
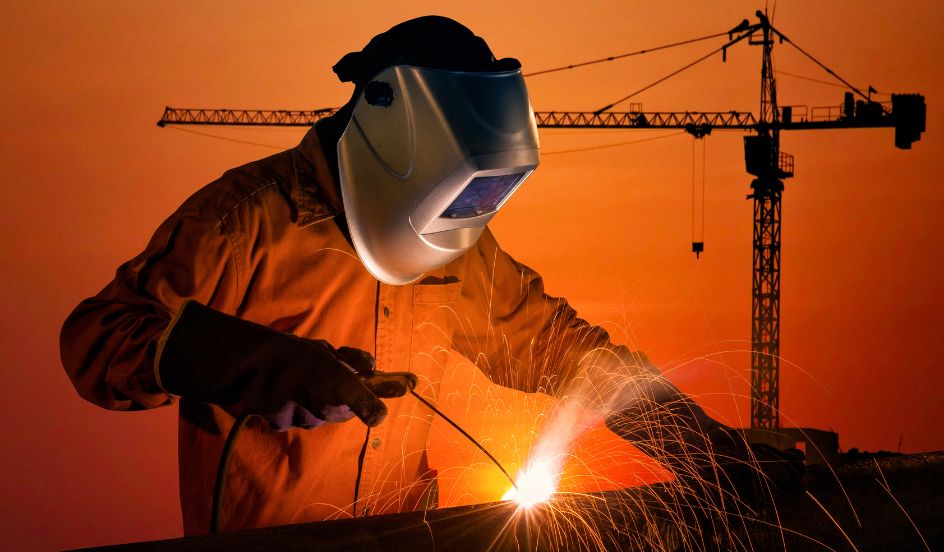
Secondly, training and credentials of welding workers according to the specific demands of the WPS is extremely important. Offering detailed training programs and making certain that welders are certified to execute procedures detailed in the WPS can result in better welds and reduced rework.
Furthermore, leveraging modern technology such as welding software and tracking systems can aid in enhancing WPS. These tools can help in monitoring variables, ensuring parameters are within specified YOURURL.com restrictions, and offering real-time comments to welders, allowing them to make prompt changes for boosted weld quality.
Common Difficulties and Solutions
Dealing with challenges in carrying out the approaches for WPS optimization can prevent welding procedures' efficiency and quality. One common obstacle is inadequate training or understanding of the welding treatment requirements (WPS) amongst the welding group. This can bring about inappropriate execution of welds, resulting in problems and remodel. To address this, extensive training programs need to be implemented to make certain that all welders excel in using and analyzing WPS properly.One more challenge is the absence of correct paperwork and record-keeping, which is vital for WPS optimization. Without clear records of welding specifications, products utilized, and evaluation results, it comes to be challenging to determine areas for you could try this out improvement and make certain consistency in welding procedures. Implementing a durable paperwork system, such as digital welding monitoring software application, can help streamline record-keeping and promote data analysis for continuous improvement.
Furthermore, inconsistent welding devices calibration and upkeep can pose a considerable challenge to WPS optimization. Regular equipment checks, calibration, and upkeep schedules must be complied with purely to make sure that welding parameters are properly regulated and preserved within the defined tolerances (welding WPS). By attending to these typical obstacles with proactive remedies, welding procedures can enhance efficiency, top best site quality, and overall welding excellence
Best Practices for WPS Implementation
To make sure effective WPS implementation in welding operations, adherence to market requirements and thorough focus to detail are extremely important. When launching WPS implementation, it is vital to begin by thoroughly understanding the certain welding demands of the project. This requires a comprehensive evaluation of the welding treatment requirements, materials to be welded, and the environmental problems in which the welding will take place.When the demands are clear, the following action is to pick the appropriate welding procedure that lines up with these requirements. This entails getting in touch with the relevant codes and standards, such as those offered by the American Welding Society (AWS) or the International Organization for Standardization (ISO), to make sure conformity and quality.
Furthermore, recording the entire WPS execution procedure is crucial for traceability and top quality control. Comprehensive records ought to be maintained regarding welding criteria, product prep work, preheat and interpass temperatures, welding consumables used, and any kind of inconsistencies from the initial treatment. Routine audits and evaluations of the WPS can help determine locations for enhancement and guarantee continuous optimization of the welding process.
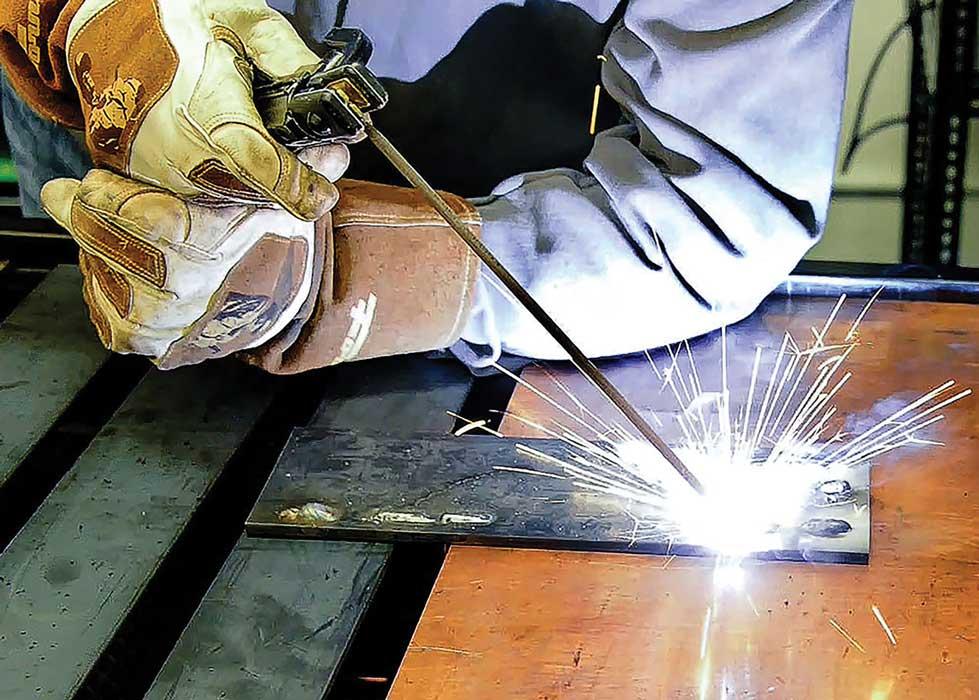

Conclusion
In conclusion, the application and optimization of Welding Procedure Requirements (WPS) is important for attaining welding quality. By understanding the key components of WPS, carrying out effective approaches for optimization, resolving common difficulties, and adhering to finest practices, welders can ensure top quality welds and secure working conditions. It is critical for experts in the welding market to focus on the correct application of WPS to boost overall welding performance and attain desired end results.
The Relevance of Welding Procedure Specs (WPS) in the welding sector can not be overstated, serving as the foundation for ensuring consistency, high quality, and security in welding operations. A WPS provides in-depth guidelines on how welding is to be brought out, consisting of essential variables such as materials, welding processes, joint design, filler metals, interpass and preheat temperatures, welding currents, voltages, traveling speeds, and much more. One critical aspect of a WPS is the welding process specification, which outlines the specific welding processes to be utilized, such as gas tungsten arc welding (GTAW) or protected metal arc welding (SMAW) By incorporating these essential components right into the WPS, welding treatments can be standardized, making sure top quality, performance, and safety and security in welding operations.
It is crucial for experts in the welding market to prioritize the proper execution of WPS to boost total welding efficiency and achieve wanted end results.
Report this wiki page